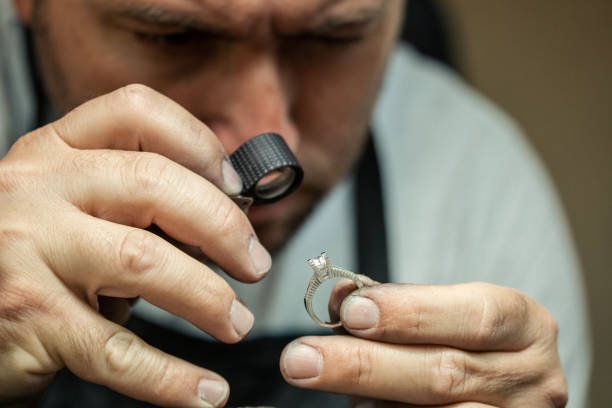
Quality Control in Jewellery-Making Machinery is essential for maintaining precision and high standards in the production of gold and silver jewellery. To produce top-quality items, ensuring that jewellery-making machinery operates efficiently is crucial. Quality control in this field involves a systematic process that covers inspection, maintenance, and testing at every stage of production, ensuring that each machine performs optimally and delivers consistent, high-quality results. This focus on quality at every step—ranging from the selection of raw materials to final product checks—helps guarantee that each piece of jewellery is made with precision and durability.
Key Areas of Quality Control in Jewellery-Making Machinery
1. Material Quality and Selection
The foundation of quality machinery lies in the raw materials used to construct it. The durability and performance of the machines depend heavily on the quality of metals and alloys chosen for the components.
- Metal Composition: High-grade steel or specialized alloys are commonly used in jewellery-making machinery due to their ability to resist wear and tear. These materials are vital for components such as rollers, molds, and gears, which face constant friction during operation. The strength of the material ensures that machinery can withstand the pressures of shaping and polishing metals like gold and silver, which can be quite demanding on equipment.
- Component Verification: Before assembly, each individual component—such as molds, rollers, and engraving tools—must undergo thorough inspection. These components are checked for imperfections such as cracks, distortions, or uneven surfaces, which could affect the machinery’s ability to perform precisely. This step is crucial, as even minor flaws in components can lead to inconsistencies in jewellery production.
2. Manufacturing Precision
The precision of jewellery-making machinery is paramount to producing high-quality pieces. If machinery is not built with accuracy, it can result in uneven products or breakdowns.
- Assembly Check: During assembly, it is vital to ensure that all parts fit together seamlessly. Misalignments or improper fittings could impact the jewellery’s dimensions, such as thickness, weight, or overall form. For example, a misaligned rolling mill could produce metal sheets that are inconsistent in thickness, which could compromise the design of the final piece.
- Testing: Before machinery is put into full operation, it must undergo testing under simulated working conditions. This allows manufacturers to identify any potential issues early, such as uneven operation or mechanical failure. Machines like rolling mills and polishing units, for example, should be tested to ensure they perform at the correct speed, power, and precision levels.
3. Regular Maintenance
Routine maintenance is essential for extending the life of jewellery-making machinery and ensuring it continues to operate smoothly. Regular upkeep prevents breakdowns and ensures that the equipment produces consistently high-quality results.
- Lubrication: Moving parts, such as rollers in a rolling mill or hinges in a casting machine, require regular lubrication. Proper lubrication reduces friction and wear, preventing premature damage to the machinery and ensuring smooth, precise movements. Over time, the lack of lubrication can cause components to seize or become misaligned, leading to costly repairs.
- Cleaning: Jewellery-making machines, particularly those used for polishing and buffing, accumulate dust, debris, and residue. Regular cleaning is necessary to maintain smooth operation. For example, polishing units can become clogged with residue, leading to an uneven finish on jewellery pieces. After each use, machines should be cleaned thoroughly to prevent this.
- Inspections: Conducting periodic inspections is vital to identify and address issues before they cause more significant problems. Checking for loose screws, worn-out belts, or corroded parts can prevent larger malfunctions. Inspections help to catch problems early, ensuring the machinery remains in top condition.
4. Calibration and Testing
Manual calibration ensures that machinery operates with the highest level of precision.
- Calibration of Rolling Mills: A rolling mill, used for flattening and shaping metal, must be calibrated regularly to ensure that it produces metal sheets of consistent thickness. Inaccuracies in calibration can lead to uneven metal sheets, which can negatively affect the overall design and quality of the jewellery.
- Testing Buffing Machines: Buffing machines are used to polish jewellery, ensuring a smooth and glossy finish. These machines need to be calibrated to deliver a uniform polish across all surfaces. Testing the buffing machines under varying conditions ensures that the machinery does not produce uneven finishes, which can be noticeable on high-end jewellery pieces.
5. Training for Operators
Even the most advanced machinery can underperform if not operated properly. Well-trained operators are essential to ensure that machinery runs smoothly and produces high-quality results.
- Skill Development: Training is vital for ensuring that workers can handle machinery like melting furnaces, casting units, and engraving tools with precision. Skilled operators understand how to adjust the machinery for optimal performance and can troubleshoot when issues arise.
- Safety Protocols: Training on safety protocols is equally important. Operators must be well-versed in how to safely handle equipment and materials to prevent accidents and damage to the machinery. Proper safety measures not only protect workers but also reduce the risk of costly machine repairs or replacements.
6. Stress and Durability Testing
To ensure the machinery can handle demanding tasks, it undergoes stress and durability testing. This testing helps identify potential weaknesses and guarantees long-lasting performance.
- Load Testing: Machines like casting units are tested to determine their capacity to handle high volumes of material. These tests simulate the conditions the machines will face during regular use, ensuring that they do not overheat or fail under heavy loads.
- Heat Resistance: For machines like melting furnaces, it’s essential to test their ability to maintain consistent, stable temperatures over extended periods. Fluctuations in temperature can affect the quality of the metal, leading to inconsistencies or defects in the jewellery.
Final Thoughts
Quality control in jewellery-making machinery is an essential process that ensures the production of high-quality gold and silver jewellery. By focusing on material selection, manufacturing precision, regular maintenance, calibration, operator training, and durability testing, jewellers can maintain the highest standards in their production lines. This systematic approach minimizes errors, reduces downtime, and guarantees that the jewellery produced is both beautiful and durable.
Are you looking to enhance the precision and durability of your jewellery-making machinery? Explore Our Products today to know more about our high-performance tools and maintenance solutions tailored to your needs.